充放電サイクル試験用ラミネート型サンプルの品質改善事例
独自の新電池を開発し、量産計画を発表されている海外の電池メーカー様からのご相談です。
充放電試験用のラミネート型電池サンプルの品質不足がご課題でした。
コインセルでの基礎的な性能評価を終えられ、より製品に近い電池サイズでの充放電サイクル試験に臨まれる段階でご相談をいただきました。
「安価で手軽である」という理由から、いわゆるトムソン型を使用してラミネート電池用の電極版を打抜いていましたが、集電箔のバリや、活物質のハガレなどを解消できずにお困りでした。
この事例のポイント
電池性能を損なわない高品質なラミネート型サンプルを安定加工!
お客様の課題
トムソン型のメリットと特性に合った用途
トムソン型(steel cut die)は、トムソン刃(帯状の剃刀の様な刃)を曲げて、得たい打抜き形状の刃を自由に作れることが利点です。その手軽さと価格の安さから、ラミネート電池用の電極版など、大きめの形状の製品を加工するために採用されることも多いツールです。
トムソン型は、例えば今後作成していくサンプル形状を決める目的で、色々なサイズで試作したいときなどには、コストとスピードの面で適しています。しかし、正確な性能データを得るための電池の試作用に、一定以上の品質を満たしたサンプルを安定して得たい場合には不向きです。
トムソン型が原理的に持つ、打抜き加工時の品質劣化の要因
トムソン型での打抜き加工は、打抜きたい形状に曲げた帯状の刃を、材料の上から、下板へと押し付けて離断させる方法です。
実際には刃の全周を完全に同じ高さに合わせて製作したり、刃を下板へ押し付けた際、全周をムラなく均一な圧力で接地させることは難しいため、材料の下にクッションとなるシート等を敷いて打抜き加工することになります。
また、刃の厚みをゼロにすることはできず、抜き型として複数回の使用できる一定の強度を持たせるためには、トムソン刃に、ある程度の厚みが必要です。
トムソン刃を下死点まで加工させ、取りたい製品の形状に離断させるためには、刃のの先端部分を鋭利に尖らせる必要があります(前述のクッションシートは、刃の先端を保護する働きもします)。
そのためトムソン刃の断面は「V」の字型となります(「レ」の字型に近づけることもできますが、強度の関係で限界あり)。
トムソン型で打抜く際、製品の外周端部、特に「V」の字型の刃の斜面が当たった状態まま、下方へと引きずられる部分の活物質が崩落します。
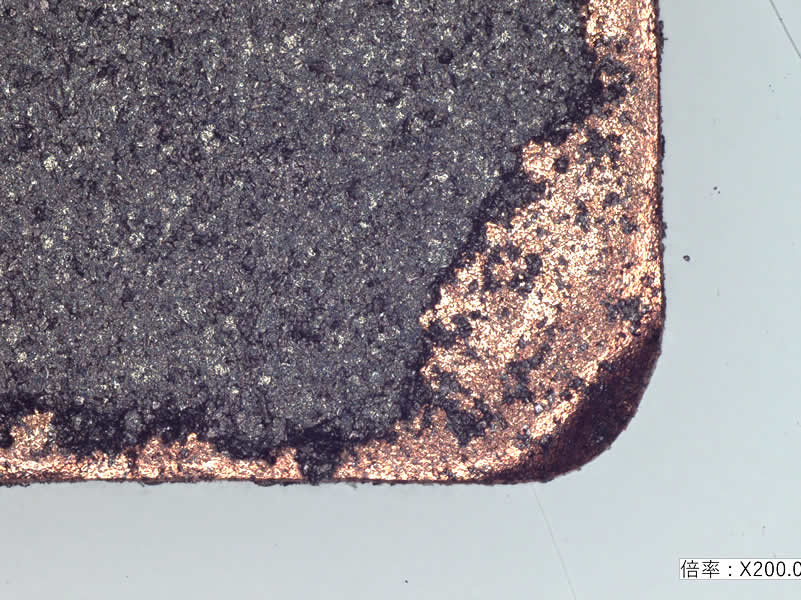
活物質の剥離・崩落が起こり、角部の基材が打抜き方向(下方)へダレ込んでいる
同時に、トムソン刃がクッションシートの層まで下降する過程で、基材も打抜き方向(下方)へと押し下げられます。そのまま下死点まで刃を下降させ、材料を千切る形で離断させるのがトムソン型です。
そのため、端面の基材(金属箔)には下方に向けてバリが発生、特に角型の製品角部には活物質と基材の層との間で剥離も発生しやすくなります。
ラミネート型サンプル加工のメインツールが必要
トムソン型での加工では、得られる品質に限界があることを、お客様は良くご理解でした。
高い品質基準(活物質の割れ・崩れ・滑落がないこと、集電箔のバリ高さが許容値以下であること)を確実に満たすメインツールとして、高精度な打抜き型が必要、とのご相談をいただきました。
また、お客様の電池開発チームがお持ちの、以後の開発スケジュール上の要請から、充放電サイクル試験の頻度を上げ、製作するサンプルの数も大きく増加させるご計画でした。
「品質要件を確実に満たすことが最重要」としながらも、サンプル製作~測定・評価プロセスの作業効率・スピードアップのご要件も満たす必要がありました。
野上技研のご提案
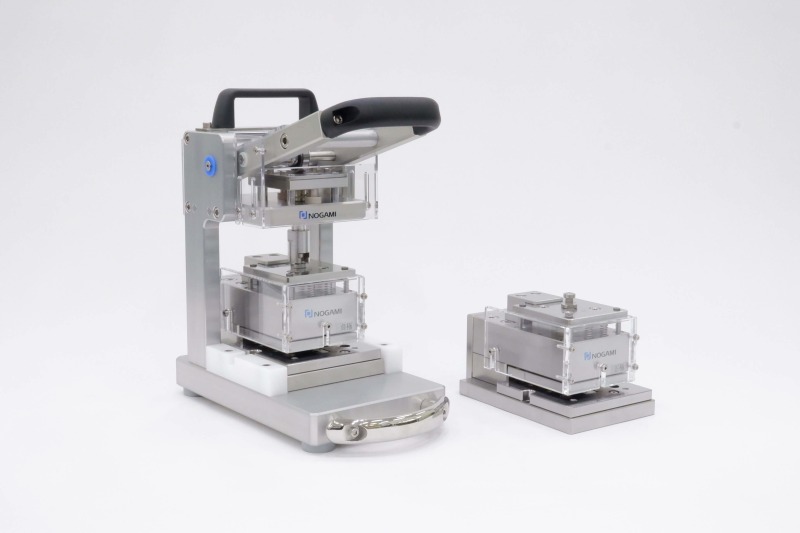
採用結果
期待を大きく上回る断面品質が得られた
お客様ご支給の材料で行ったテスト加工の結果レポートをご覧いただいた段階で、活物質の破壊・崩落、集電箔のバリ共に、「NOGAMIのツールなら、要求品質を完全に満たした加工が可能」とのコメントをいただけました。
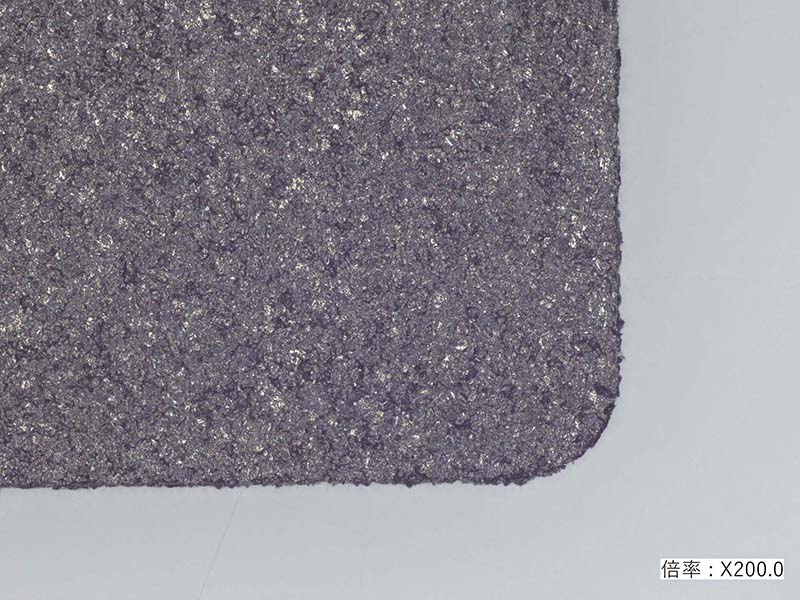
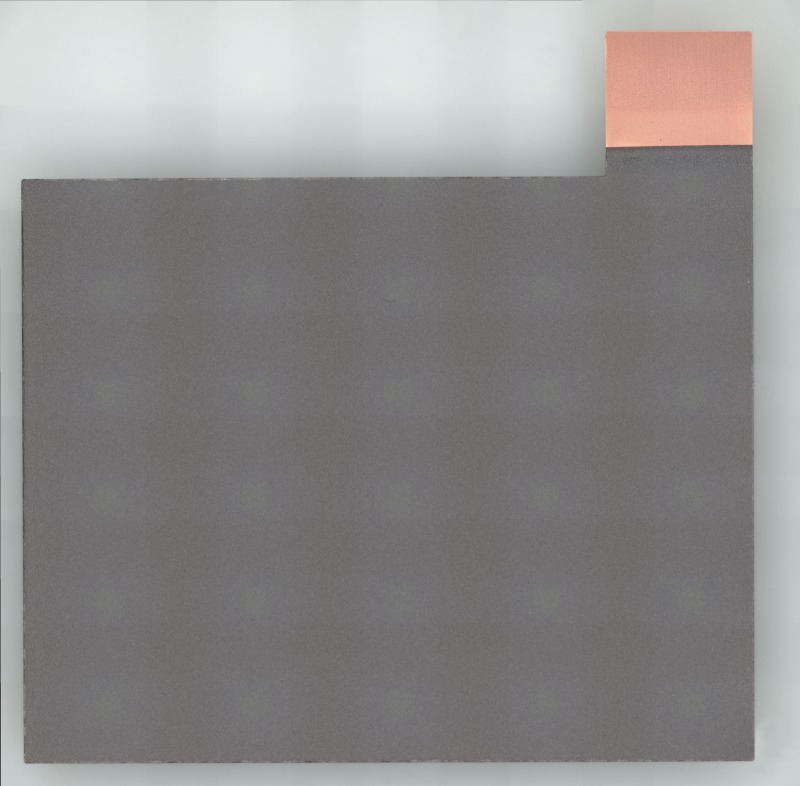
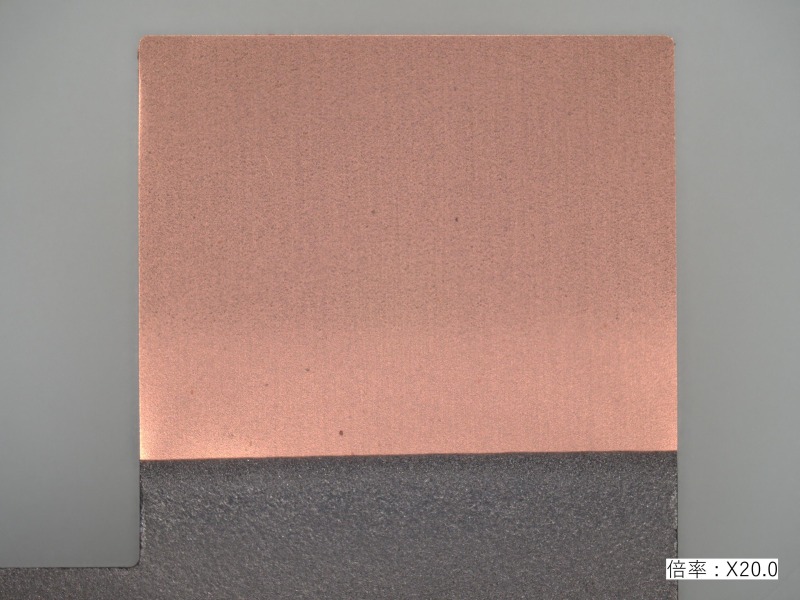
活物質がコーティングされた外周すべて、基材の銅箔が露出した集電箔の部分ともに、「事前の期待を大きく超える、良好な品質だった」とのことです。
作業性も格段に上がった
もう一つの懸案だった作業のし易さ、加工スピードの面でも、Cフレーム構造の卓上治具『クリーンプレス』の使い勝手は、高くご評価いただけました。
コンパクトで軽量なため、お一人でもグローブボックスに出し入れができ、狭いグローブボックス内での作業も、ストレスなく行えるようになりました。
以前のトムソン型の場合、加工する毎に一回、一回、製品をピックアップする必要があります。
時に、加工した製品が刃に食い付いてしまい、抜き落せないこともあります。トムソン刃に食い付いて落ちない製品をピンセットで外す際、製品を傷つけたり、変形させてしまったりするケースもありました。
精密なせん断加工の動作と刃の切れ味を持つクリーンプレスの採用後、製品の食い付きはなくなりました。
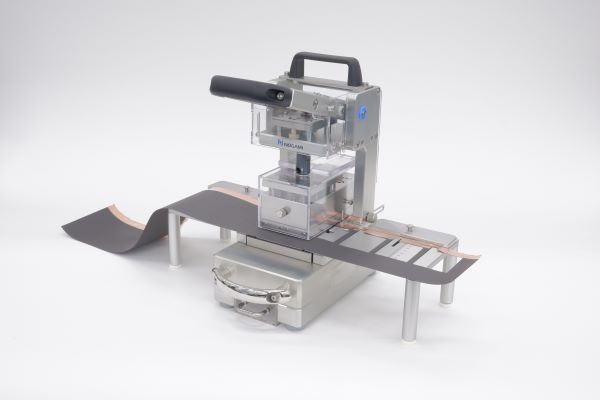
打抜いた製品は、自重でクリーンプレス底面の回収ボックスに落ちるため、
「開口部へ横から材料をセットして打抜き、また材料を横に送って位置を決め、また打抜き・・・」
という、材料を送りながらの連続加工が可能です(深さ27㎜の回収ボックスには、200μmの電極版なら135枚回収可能)。
回収ボックスを取り外して数百回、続けて加工することもできます。
シンプルで無駄のない連続加工の作業手順は、ハンドリングのミスをなくし、大きなスピードアップに繋がりました。
また、作業者の方の安全性の面でも、「作業時も治具の出し入れにおいても、このツールによって誰かが怪我をする余地がそもそもない」とのお言葉をいただけました。
お客様のコメント
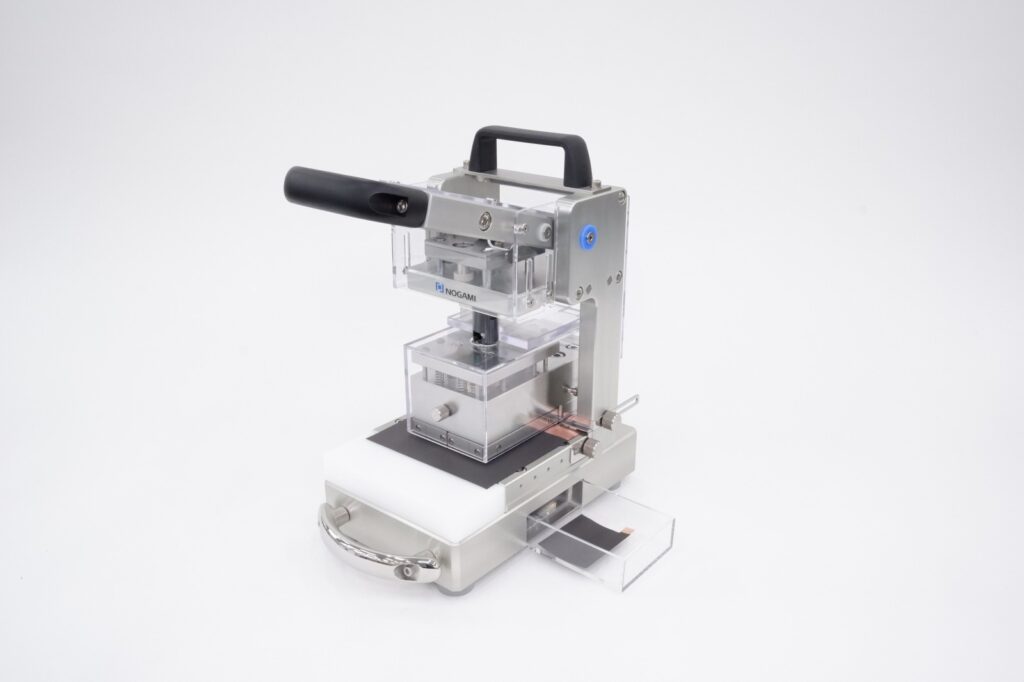